India Cements to upgrade plants, sell non-core assets
Chairing the 77th annual general meeting, Srinivasan told the shareholders that the company’s last year performance was severely dented
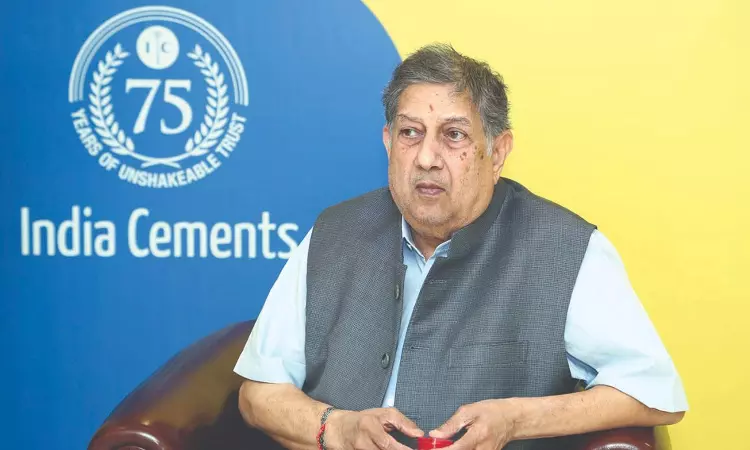
N Srinivasan, Vice Chairman and Managing Director, India Cements
CHENNAI: Cutting down the variable costs by upgrading its plants, selling off and non-core assets to manage the cash position are the two strategies followed by cement major India Cements Ltd, Vice Chairman and Managing Director N Srinivasan said on Thursday.
Chairing the 77th annual general meeting, Srinivasan told the shareholders that the company’s last year performance was severely dented on account of significant increase in input cost, supply overhang, tough market conditions with severe competition and subdued price realisation resulting in drop in margins and due to one off expenses on account of provision for impairment for certain investment and advances.
“With a basket of plants of various vintage and technology with varying operating parameters of power and fuel, the impact on cost of production on account of steep increase in coal price, diesel, pet coke, power, etc. was much higher for the company as compared to many of the peers,” he said.
“With lower capacity utilization of 64 per cent during the year and blended cement proportion accounting for only of 50 per cent in the overall sales mix due to increased infra-activity in South, the margins were squeezed with uncompensated cost increase,” he added. On the operational front, cost per Kcal of fuel increased to Rs 2.90 from around Rs 1.85 in the previous year and average rate of power went up by 35 per cent to Rs 7.04 per KWH from Rs 5.20 per KWH.
These two major factors together with reduction in blended cement proportion increased the cost of production by more than Rs 840 per tonne or 31 per cent over the previous year.
The net plant realisation improved hardly by Rs 200 per tonne resulting in substantial erosion in profit margin. This together with all the factors mentioned above resulted in a negative EBIDTA of Rs 140 crore as compared to EBIDTA of Rs 478 crore in the previous year, Srinivasan said. According to him, the variable costs continue to be high for India Cements compared to peers and the company has initiated necessary action to address the same. The new Cement Mill at Sankar Nagar in Tamil Nadu replacing the old cement mills, is expected to be commissioned by 2nd quarter of the current fiscal.
“The waste heat recovery system at Chilamkur in Andhra Pradesh is also being taken up for completion during the current year and both these projects are expected to bring in substantial relief in variable cost in the two plants,” he said. The company has engaged the services of experts like FLSmith and ThyssenKrup Industries to conduct a detailed study on the operating parameters of some of its plants for refurbishment/modernisation to bring them in line with that of state-of-the-art modern plants.
The company has engaged Boston Consulting Group to study the operations at three of its plants in Andhra Pradesh and Telangana and suggest measures for improving efficiency in their operations, Srinivasan said.